C混凝土无处不在:建筑物、道路、人行道、桥梁以及几乎所有可以想象到的结构的基础中都有混凝土。我们生产的混凝土比地球上任何其他材料都多,而且由于全球发展,尤其是在中国和印度,这个产量还在上升。水泥——将混凝土中的沙子或碎石粘合在一起的粉状粘合剂——是地球上能源密集型最高的产品之一。水泥中使用的石灰石在巨大的窑炉中被烘烤到高达 1,450 摄氏度(2,640 华氏度)的温度,这些窑炉几乎完全使用化石燃料进行加热。所涉及的化学反应产生更多的二氧化碳作为副产品。每生产一公斤水泥,就会向大气中排放一公斤二氧化碳。在全球范围内,水泥和混凝土生产每年产生的二氧化碳排放量高达人类二氧化碳总排放量的 9%。
一个世纪以来,社会制造水泥和混凝土的方式几乎相同。试验表明,混合物中的一部分水泥可以用煅烧(烧过的)粘土或废料(如粉煤灰和矿渣)制成的成分代替,强度不会降低,但排放量会减少。替代品的供应不足以满足需求,但这些替代品可以在一定程度上减少二氧化碳排放。
其他替代材料和工艺可以显着减少排放。有些已经在普及;另一些则处于实验阶段。由于大多数水泥和混凝土都是在当地或地区生产的,靠近使用地点,因此替代材料的可用性、允许使用替代材料的修订后的建筑标准、重新装备的资本成本以及市场接受度都是实际的挑战。
关于支持科学新闻
如果您喜欢这篇文章,请考虑通过以下方式支持我们屡获殊荣的新闻报道 订阅。通过购买订阅,您正在帮助确保未来能够持续报道关于塑造我们当今世界的发现和想法的具有影响力的故事。
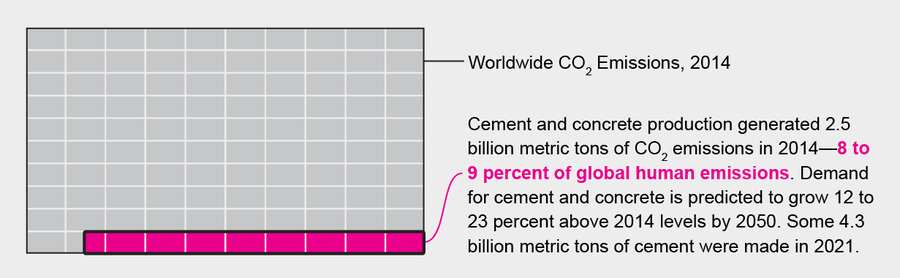
图片来源:Jen Christiansen
更优的水泥生产
水泥制造消耗大量能源,其中大部分来自排放二氧化碳的化石燃料。某些步骤也会直接排放二氧化碳,特别是石灰的生产(步骤 3)和熟料(一种硬化剂)(步骤 4)。用可再生能源替代化石燃料并提高整个生产过程的效率可以将碳足迹减少高达 40%。使用不同的熟料原材料可以大幅降低剩余 60% 的碳排放量。(所示过程适用于所谓的干法窑;它们已广泛取代湿法窑,湿法窑使用更多的能源。)
1. 开采和研磨石灰石
工作原理:含有碳酸钙的矿藏,如石灰石或白垩,是从采石场开采的,其中可能包含少量含有硅、铝或铁的粘土。将这些成分压碎成小于 10 厘米的碎片,然后研磨成称为生料的粉末。
改进空间:从玄武岩而不是石灰石开始,或使用用废二氧化碳生产的“负碳石灰石”(步骤 2),减少排放量达 60% 至 70%。
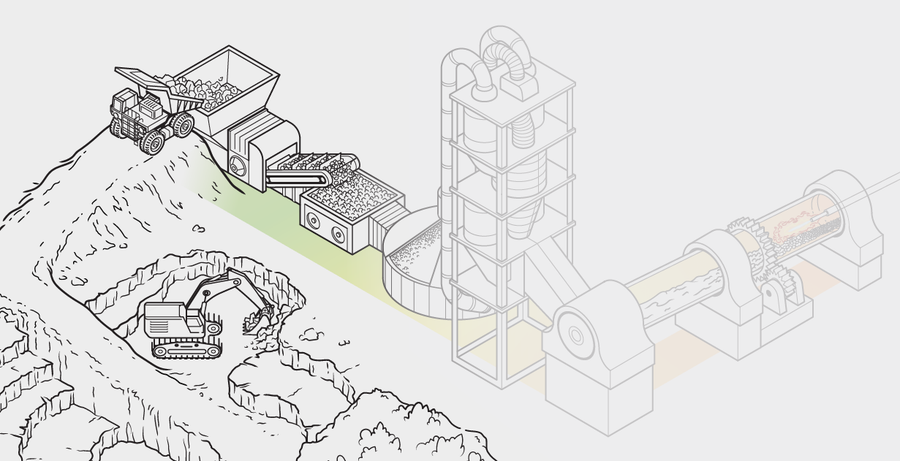
图片来源:Nick Bockelman
2. 预热生料...
工作原理:窑炉上方腔室中的生料被窑炉的高温、旋转的废气加热到高达 700 摄氏度的温度,从而驱除水分。
改进空间:燃烧富氧空气以减少二氧化碳排放。添加设备以捕获二氧化碳,这可以将排放量减少高达 60%。使用废二氧化碳制造负碳石灰石(步骤 1)。燃烧生物质或废物来加热窑炉,而不是化石燃料。
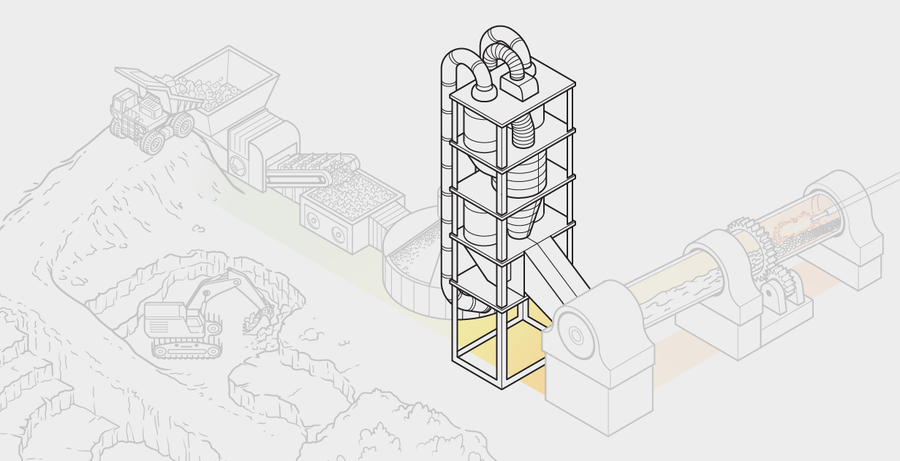
图片来源:Nick Bockelman
3. ...并将生料转化为石灰
工作原理:预热后的生料在窑炉顶部上方和内部的燃烧室中以 750 至 900 摄氏度的温度燃烧,将碳酸钙转化为氧化钙(生石灰)和二氧化碳。此步骤占原材料中二氧化碳排放量的 60% 至 70%,并消耗整个水泥生产过程中约 65% 的燃料。
改进空间:燃烧富氧空气以减少二氧化碳排放。添加设备以捕获二氧化碳。使用可再生能源驱动的电窑,将步骤 2、3 和 4 的排放量减少 30% 至 40%。
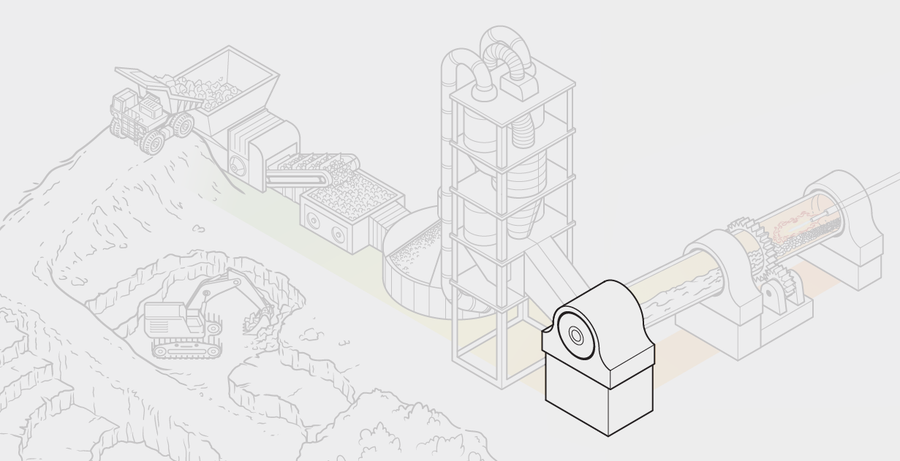
图片来源:Nick Bockelman
4. 将石灰转化为熟料
工作原理:石灰在以每分钟三到五转的速度旋转的窑炉中以高达 1,450 摄氏度的温度燃烧。此过程将石灰烧结(熔合)成波特兰水泥熟料——直径为 3 至 25 毫米的深灰色结核——并驱除更多的二氧化碳。熟料是水泥与水反应时使其硬化的粘合剂。
改进空间:添加矿化剂,如氟化钙或硫酸盐,以降低石灰的烧结温度,从而节省能源。
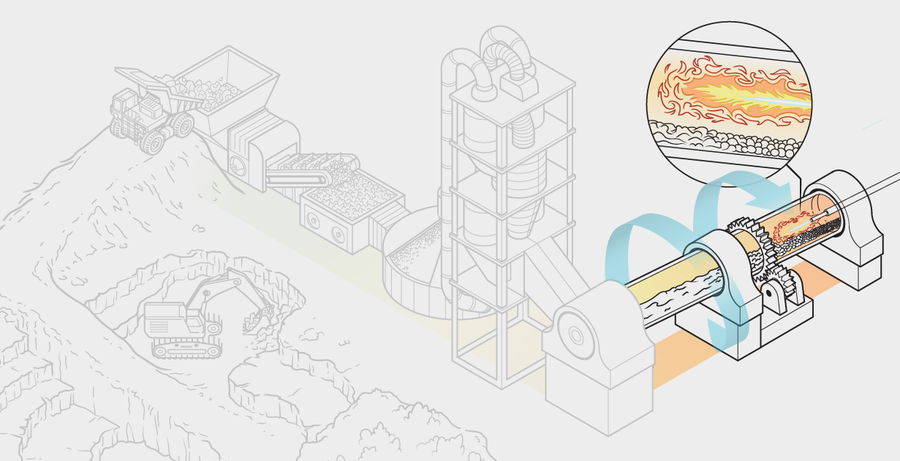
图片来源:Nick Bockelman
5. 冷却和储存熟料
工作原理:热熟料在格栅上运行,空气鼓风机将其冷却至约 100 摄氏度。冷却后,将其储存在筒仓中,可以长时间保存而不会降解,因此可以作为自己的商品出售。
改进空间:将该过程电气化,或从步骤 3 引入废热用于初始冷却。
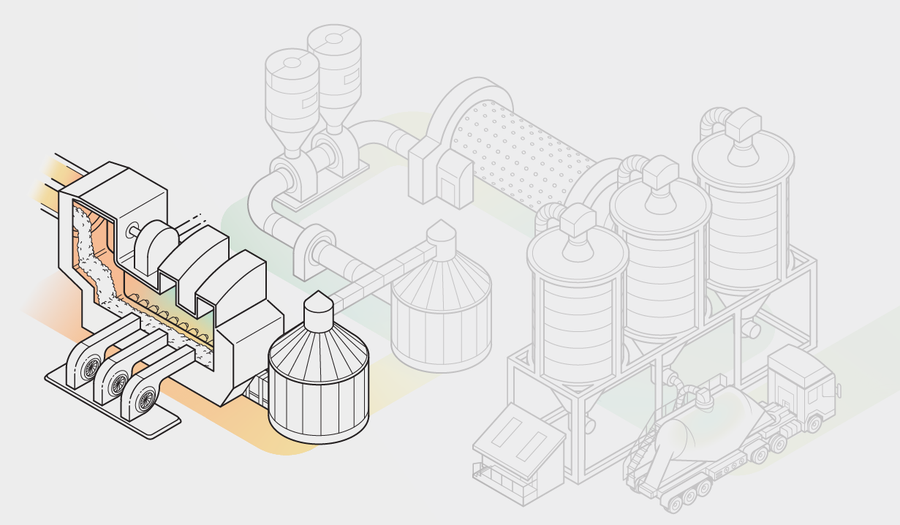
图片来源:Nick Bockelman
6. 将熟料与石膏混合
工作原理:熟料与石膏以 20 或 25 比 1 的比例混合。
改进空间:将该过程电气化。
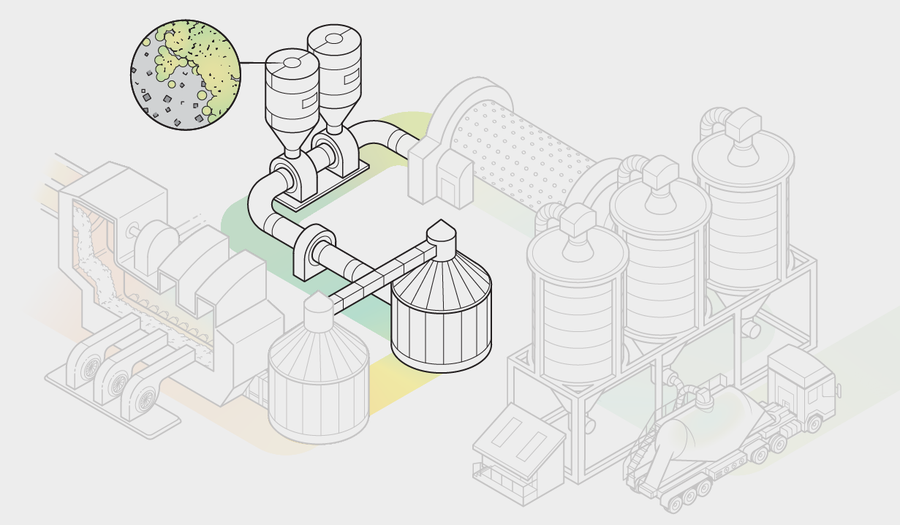
图片来源:Nick Bockelman
7. 将混合物研磨成波特兰水泥
工作原理:滚磨机或球磨机将熟料和石膏研磨成称为波特兰水泥的细灰色粉末。
改进空间:添加细磨石灰石以替代高达 35% 的水泥,从而减少早期生产步骤中产生的排放。这种混合物被称为波特兰石灰石水泥。通过添加粉煤灰(20% 至 40%)、矿渣(30% 至 60%)或煅烧粘土(20% 至 30%)来降低熟料与水泥的比例,从而创建“混合水泥”,从而将排放量减少相似的百分比。
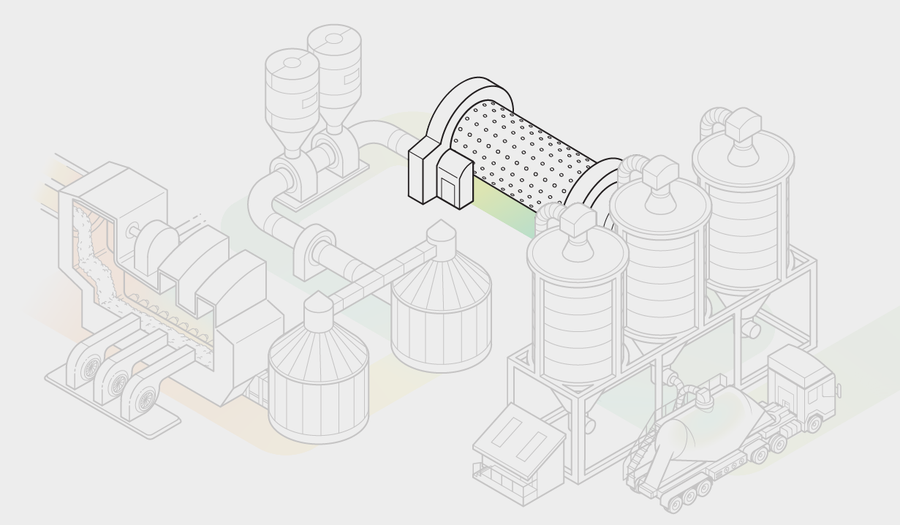
图片来源:Nick Bockelman
8. 将水泥存放在筒仓中
工作原理:将粉末充分混合,使其均匀一致,然后储存在筒仓中。它将被包装成袋装用于零售,或装载到运往混凝土搅拌站的卡车上。
改进空间:考虑使用低碳替代品来替代某些应用中的波特兰水泥。这些替代品包括碱激活水泥和藻类或微生物产生的生物水泥,以及由磷酸镁、铝酸钙或硫铝酸钙制成的水泥。这些选择可以将整个过程的排放量减少 40% 或更多。
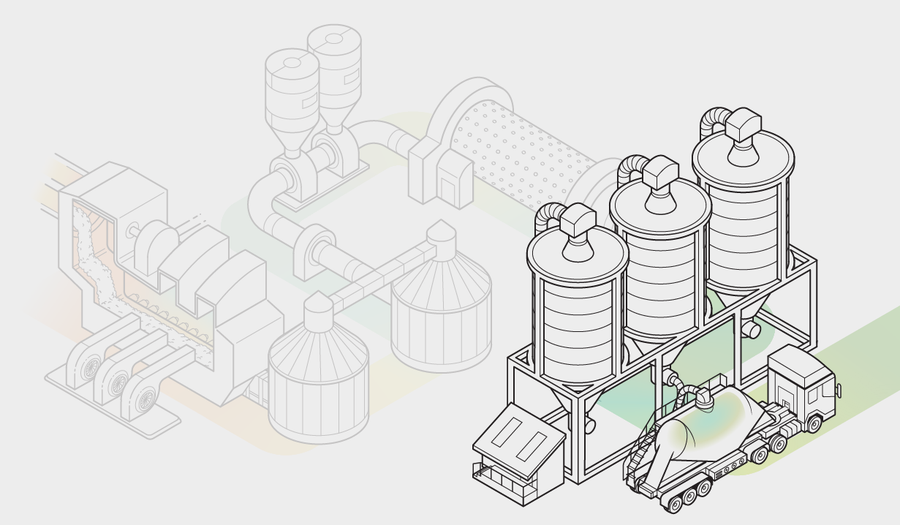
图片来源:Nick Bockelman
更优的混凝土生产
混凝土通常在建筑工地或附近生产。优化结构设计可以减少所需的混凝土量(步骤 3)。拆除后重复使用和加工混凝土(步骤 4)可以吸收大气中的二氧化碳,从而抵消原始水泥生产中的一些排放。
1. 混合水泥、水和骨料
工作原理:水泥与特定量的水和骨料(如沙子、砾石或碎石)在环境温度下混合,直到达到所需的流体稠度。混合物中约 80% 是骨料。
改进空间:将输送机和搅拌机改为使用可再生电力运行,从而大大减少排放。加入生物炭或藻类等添加剂以提高混凝土的强度或调整其工作性或凝固时间,从而将排放量减少 1% 至 5% 或更多。
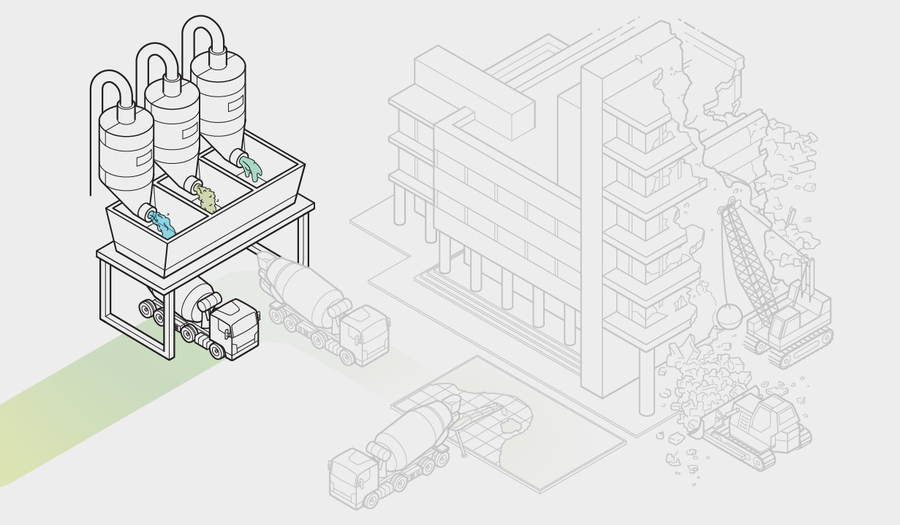
图片来源:Nick Bockelman
2. 运输到工地
工作原理:混凝土在滚筒搅拌车内混合,然后运送到建筑工地。
改进空间:改用电动卡车。最大限度地减少、收集和升级回收废弃混凝土,制成其他预制材料,如高速公路护栏。
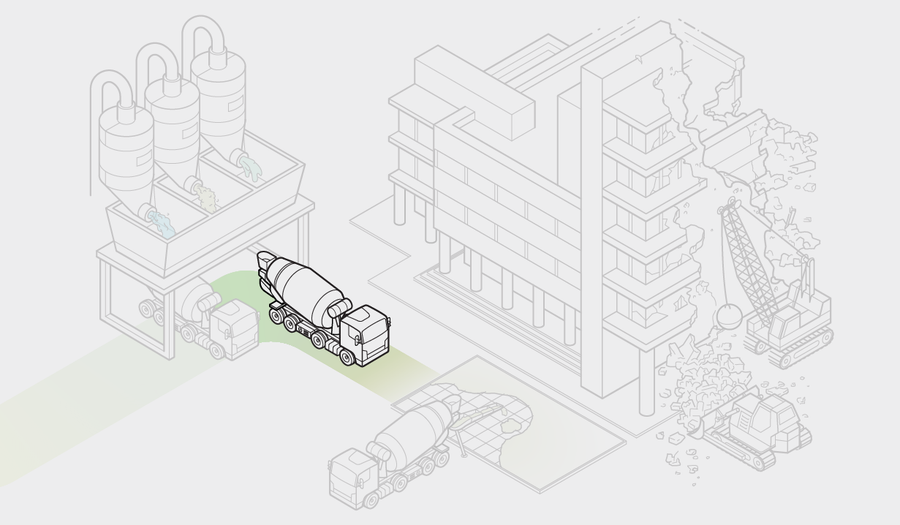
图片来源:Nick Bockelman
3. 建造结构
工作原理:建筑设计决定了所需混凝土构件的形状、体积和强度。
改进空间:优化结构设计,避免浪费混凝土。将规范从要求混凝土中水泥的最低用量更改为要求给定的抗压强度,这可以减少必要的水泥含量。修改建筑规范以允许使用新型、替代和混合水泥。依靠混凝土随时间推移获得强度的能力,通过指定两个月或三个月而不是通常一个月的抗压强度,这可以减少所需的材料量。
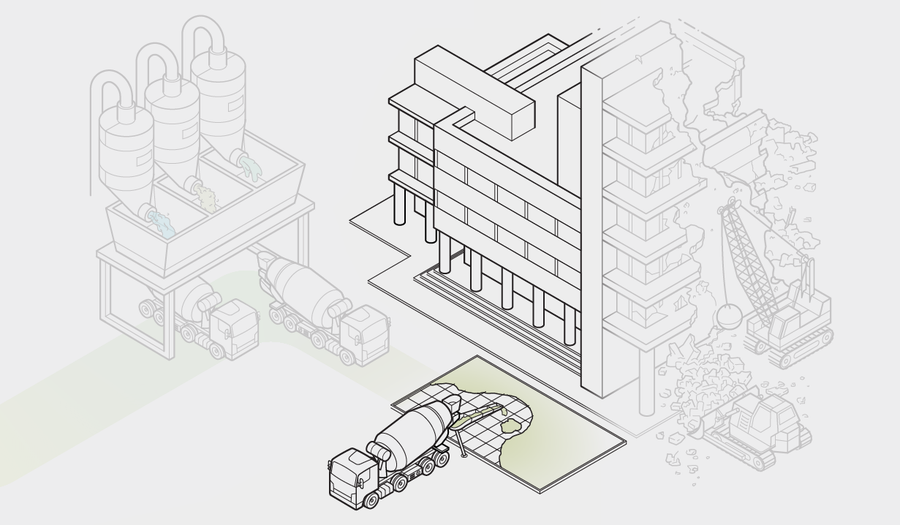
图片来源:Nick Bockelman
4. 规划报废
工作原理:拆除的混凝土通常被倾倒在垃圾填埋场或粉碎后用作道路和高速公路的基础材料。
改进空间:为拆卸而设计,以便混凝土构件可以全部或部分重复使用。如果混凝土被拆除,则将其研磨并薄薄地铺开,以最大限度地扩大其表面积并将其尽可能长时间地暴露在空气中以吸收二氧化碳。经过多年的暴露,混凝土可以吸收可能高达水泥制造时排放的二氧化碳量的 17%。
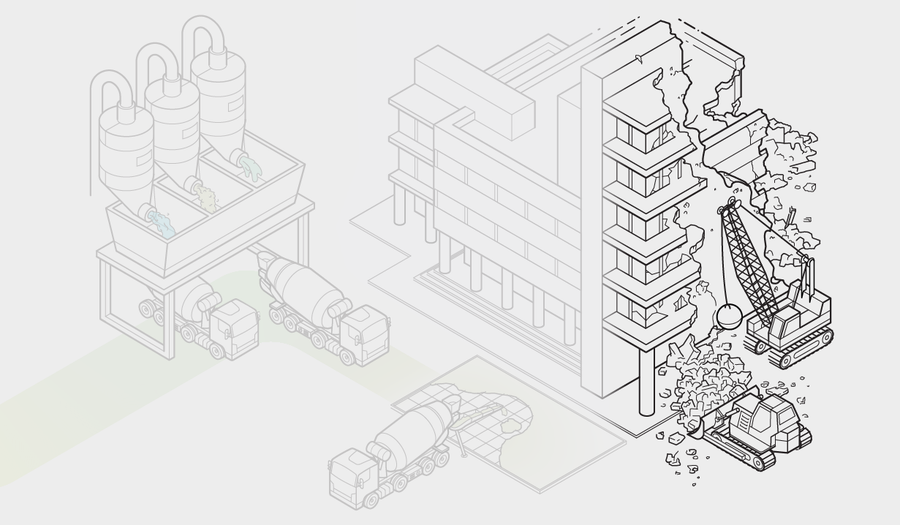
图片来源:Nick Bockelman
编者注(2023 年 3 月 30 日):本文在发布后进行了编辑,以更正石灰转化为熟料的方式的描述。